To właśnie w pobliżu stolicy Dolnego Śląska, w podwrocławskich Biskupicach Podgórnych, zlokalizowana jest fabryka LG Energy Solution Wrocław. Jej budowa rozpoczęła się w 2016 r. i pochłonęła 3,2 mld euro. Dzisiaj to niemałe miasteczko rozlokowane wzdłuż ulic LG, Seulskiej, Koreańskiej i Innowacyjnej. Na jego terenie kursuje kilka linii zeroemisyjnych minibusów, są także kantyny, sklepy z koreańskimi produktami, jednostka straży pożarnej, a już wkrótce powstanie przedszkole. Obecnie w fabryce pracuje ponad 10 tys. osób z ponad 13 krajów, a obszar jaki zajmuje przekracza 100 hektarów. Pracowników do zakładu wozi 41 specjalnych linii autobusowych.
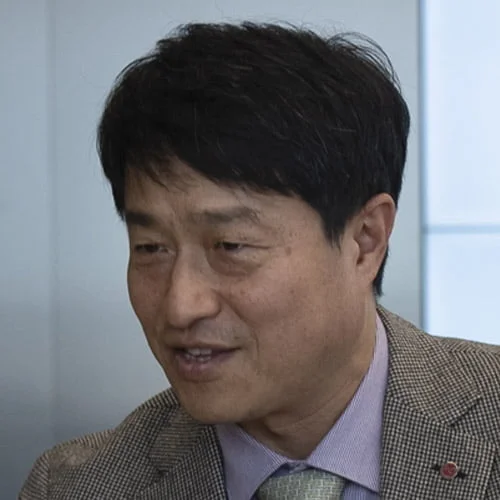
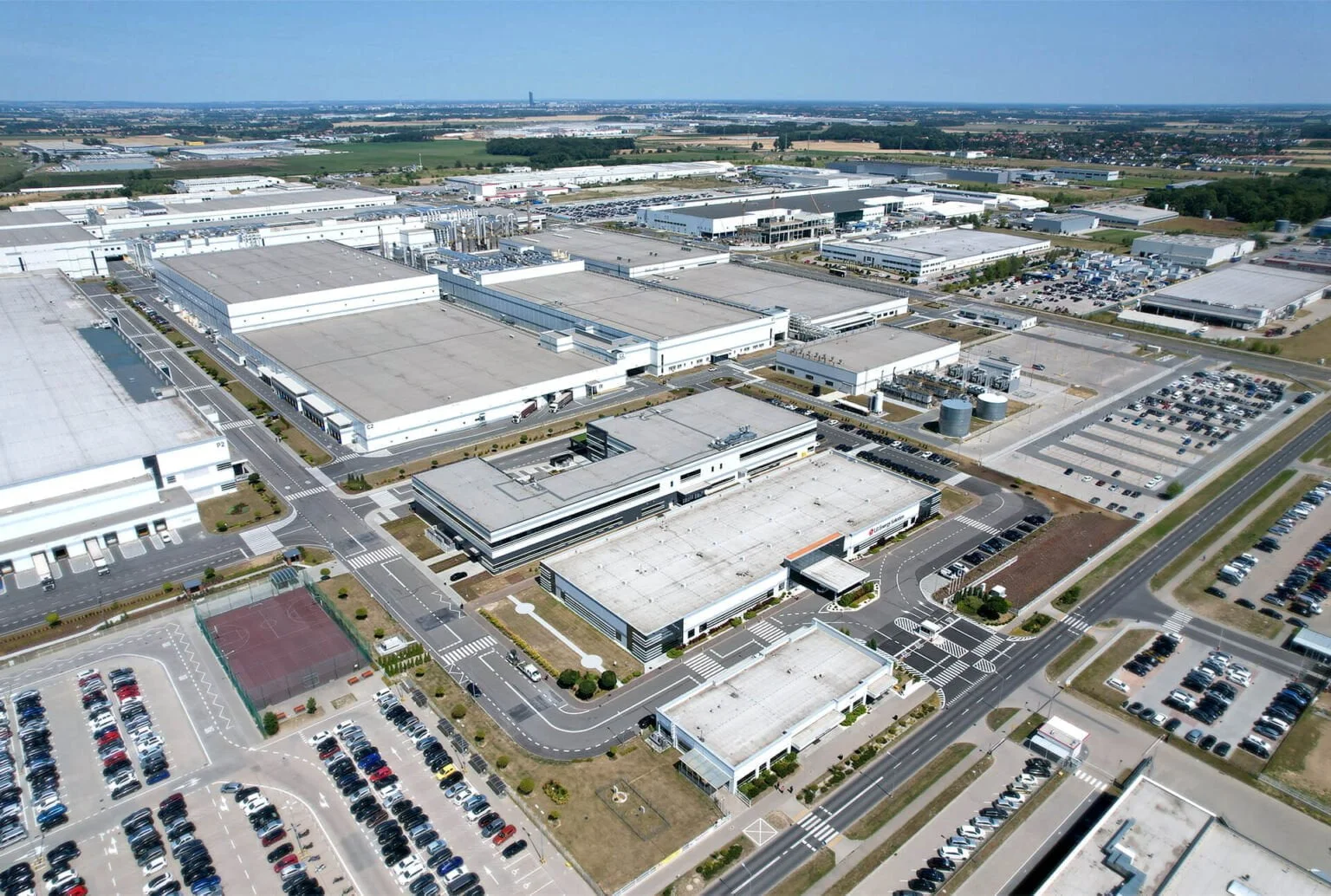
LG Energy Solution Wrocław to obecnie największe zakłady produkcyjne na terenie Europy, które do 2025 r. roku osiągną pełnię mocy produkcyjnych, czyli 115 GWh rocznie (obecnie jest to 70 GWh). Fabryka w 2022 r. może dostarczać baterie do 700 tys. aut elektrycznych rocznie, a za trzy lata planuje osiągnąć okrągły milion. Do końca tego roku producent chce uzyskać 86 GWh zdolności produkcyjnej.
Polska jest potęgą
Inwestycja w Polsce akumulatorowego giganta umieściła nasz kraj w europejskiej i światowej czołówce. Akumulatory litowo-jonowe stanowią ponad 2% całego polskiego eksportu. Jego wartość w sektorze bateryjnym wzrosła z ok. 1 mld zł w 2017 r. do blisko 30 mld zł w roku 2021. Oznacza to, że w ciągu zaledwie 5 lat, polski eksport w sektorze akumulatorów li-ion wzrósł 30-krotnie. W Polsce zakłady produkcyjne ulokowało kilka przedsiębiorstw, oprócz LG Energy Solution Wrocław także: BMZ Poland, Mercedes-Benz Manufacturing Poland, Impact Clean Power Technology, Northvolt Poland, Wamtechnik, Ele-DriveCo, SK Innovation, Capchem, Umicore, GTHR – GUOTAI-HUARONG Poland, LS EV Poland, SK Nexilis, Foosung Poland.
Dzisiaj najwięksi producenci akumulatorów są zlokalizowani w regionach, w których kupuje się najwięcej pojazdów elektrycznych, czyli w Azji, Europie i Ameryce Północnej. Prym wiodą Chiny, odpowiedzialne za produkcję 80% ogniw litowo-jonowych na świecie. Europa stawia jednak od dłuższego czasu na skrócenie łańcucha dostaw i budowę lokalnego, zrównoważonego rynku akumulatorów. Polska jest liderem łańcucha dostaw baterii litowo-jonowych w Europie i utrzyma tę pozycję co najmniej do 2025 r. Zajmuje również wysokie 4. miejsce globalnie.
Trochę historii
Sukces firmy nie jest oczywiście przypadkowy. Jej historia sięga 1947 r., kiedy powstała koreańska spółka Lucky Chemica, produkująca na początku… kosmetyki. LG Energy Solution w ciągu następujących dekad rozwinęło się na tyle, że od 1969 r. firma jest notowana na koreańskiej giełdzie papierów wartościowych. Obecnie producent zalicza się do światowej czołówki dostarczycieli baterii litowo-jonowych dla pojazdów elektrycznych, produktów IT i elektronarzędzi oraz do systemów magazynowania energii. Masowa produkcja cylindrycznych baterii Li-Ion w LG rozpoczęła się w 1999 r. Rok później rozpoczęła się produkcja dla przemysłu motoryzacyjnego, a dekadę później dostarczono pierwsze produkty do pojazdów hybrydowych (HEV). Odbiorcą była spółka Hyundai Motors. Również w 2009 r. LG podpisało kontrakt na dostawę akumulatorów dla General Motors. Były one montowane w model Chevrolet Volt. W 2000 r. postanowiono rozdzielić produkcję baterii od pozostałej działalności firmy. Z tego względu utworzono LG Energy Solution. Obecnie firma współpracuje z największymi koncernami. Największym odbiorcą jest Grupa Volkswagen.
Jak to jest zrobione?
W trakcie Open Media Day w Biskupicach Podgórnych otrzymaliśmy możliwość zwiedzenia fabryki. Poruszaliśmy się po specjalnie wytyczonej trasie, a aparaty naszych telefonów zostały zaklejone, żeby chronić to, co jest tajemnicą przedsiębiorstwa.
Choć każdy z nas słyszał o akumulatorach w samochodach elektrycznych, to mało kto wie, jak są one zbudowane. Wizyta w zakładach nieco to wyjaśnia. Na wstępnie trzeba wskazać, że akumulatory do samochodów elektrycznych są wytwarzane z kombinacji surowców. Metale „bazowe”, takie jak aluminium, miedź i żelazo, są ważnymi składnikami, ale najdroższymi materiałami są metale „szlachetne” (tzw. metale ziem rzadkich), do których zalicza się: kobalt, nikiel i mangan, grafit czy lit. Ich łączenie pozwala na stworzenie podstawowego elementu akumulatora trakcyjnego, czyli ogniwa składającego się z anody, separatora (jonoprzepuszczalna membrana – zapobiegająca zwarciu) i katody, które następnie są zalewane elektrolitem (przewodnik). Elektrolit nie musi być cieczą. W zależności od typu akumulatora może być żalem lub klasycznym ciałem stałym. W zakładach LG Energy Solution, proces ten przebiega w oddzielnej hali produkcyjnej, gdzie zachowane są sterylne warunku produkcji niczym na sali operacyjnej.
Wytworzone ogniwo (popularnie nazywane z ang. cell), jest transportowane do kolejnej hali, gdzie jest składane w moduł. Przeważnie na moduł składa się około 12 lub więcej ogniw. LG Energy Solution Wrocław dostarcza m.in. ogniwa do akumulatorów Volkswagena ID.3 i ID.4.
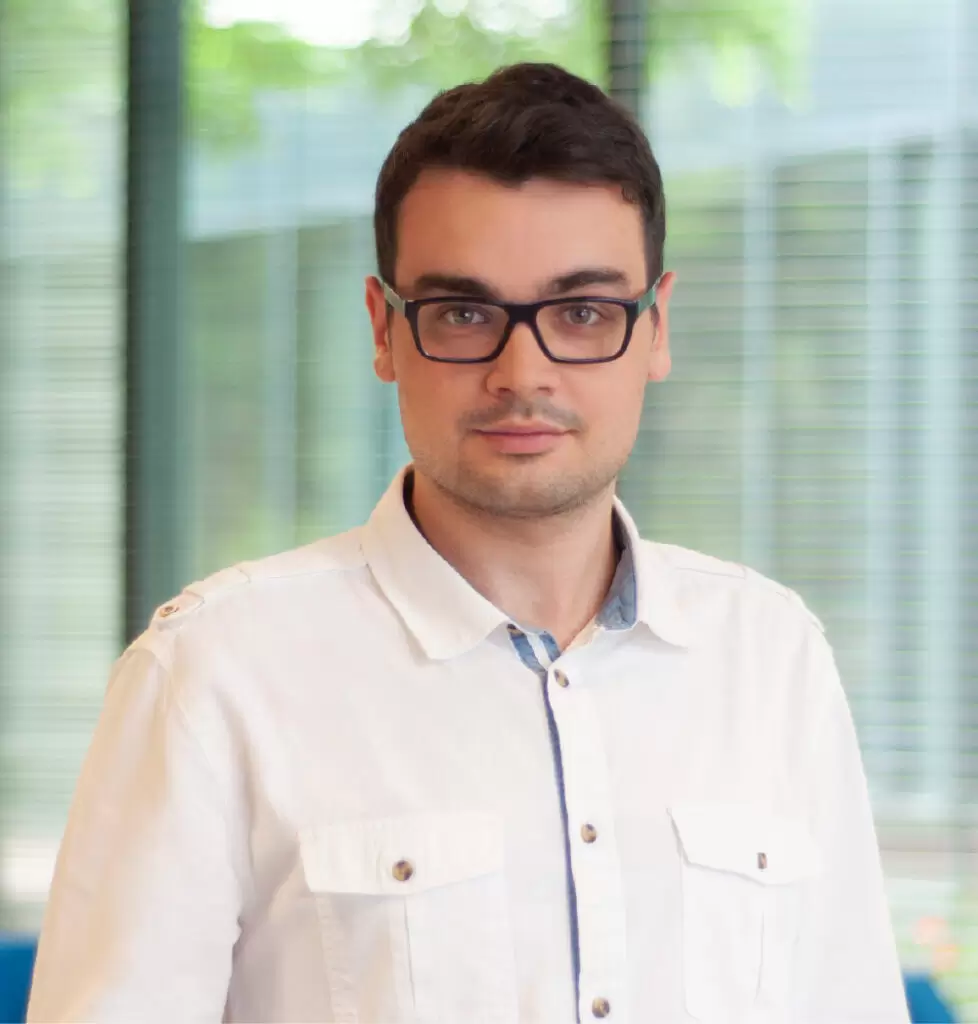
Na tym etapie, czyli jest tworzenia modułu, następuje także rozdzielenie produkcji. Wynika to z faktu, że nie wszyscy kontrahenci chcą otrzymywać gotowy produkt. Wielu z nich decyduje się na pakowanie modułów we własnym zakresie. Przy linii produkcyjnej modułów, które nie są pakowane wymagana jest mniejsza liczba obsługi. Więcej osób pracuje w sekcji, gdzie tworzone są całe paki. Posiadają one różną liczbę modułów, zależną od potrzeb pojemności baterii – jak łatwo się domyślić, większa liczba modułów powiększa pak bateryjny. Najcięższe zestawy składane pod Wrocławiem mają masę około 600 kg.
4 etapy budowy baterii
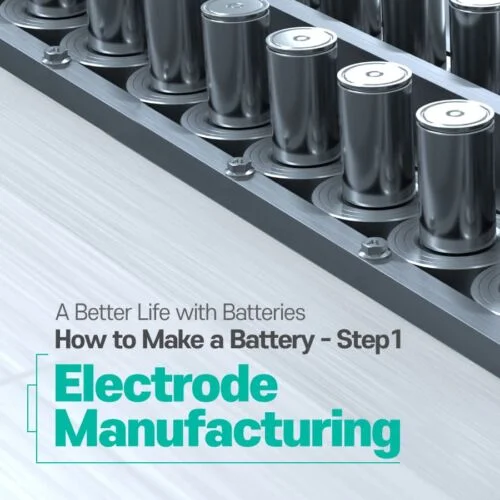
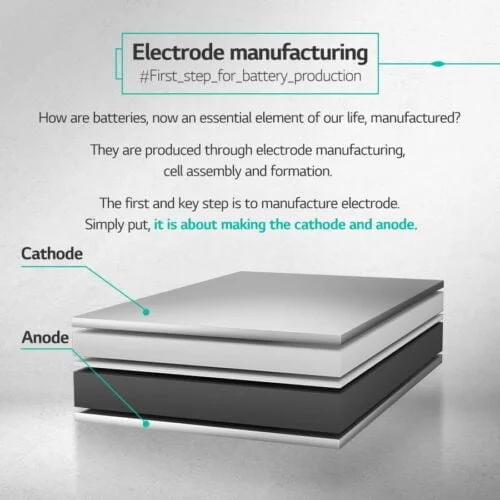
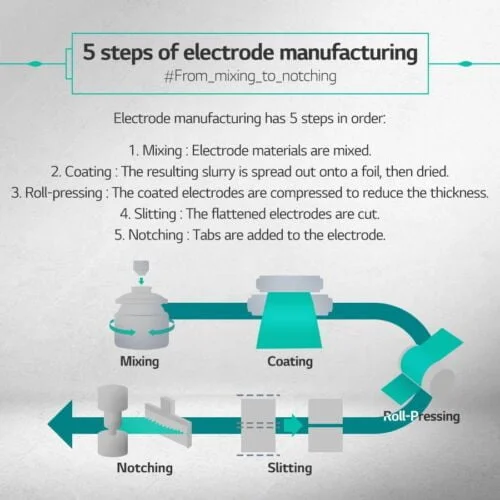
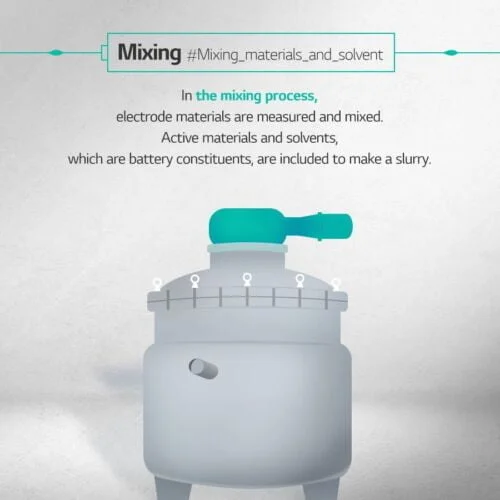
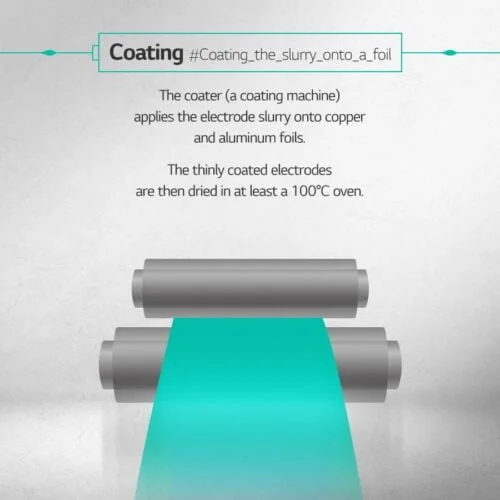
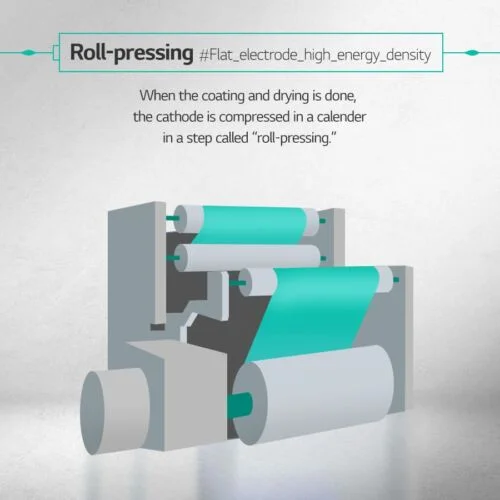
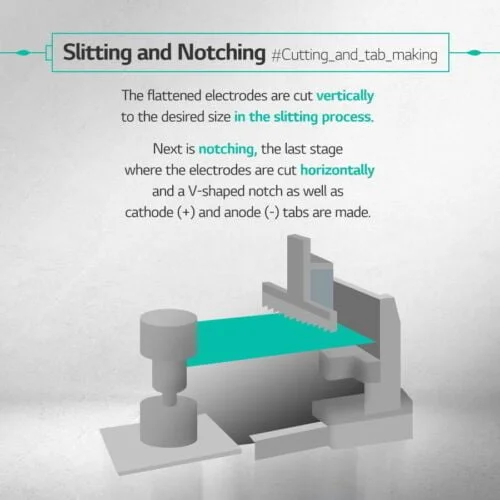
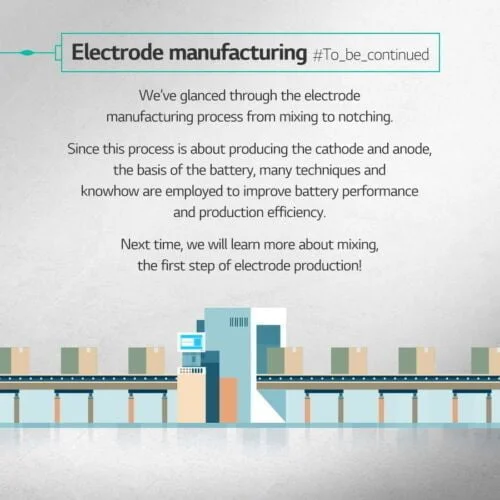
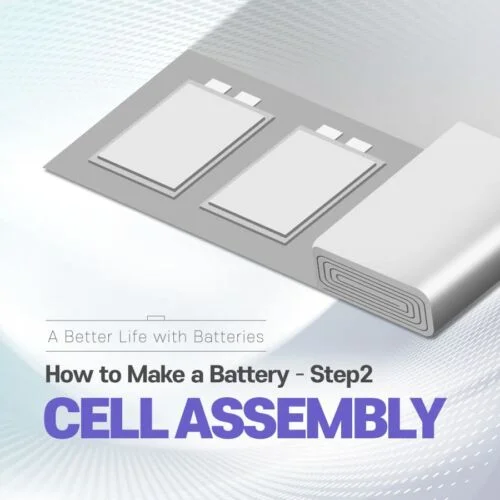
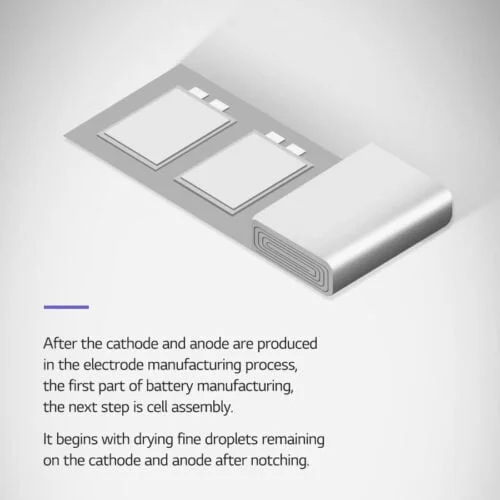
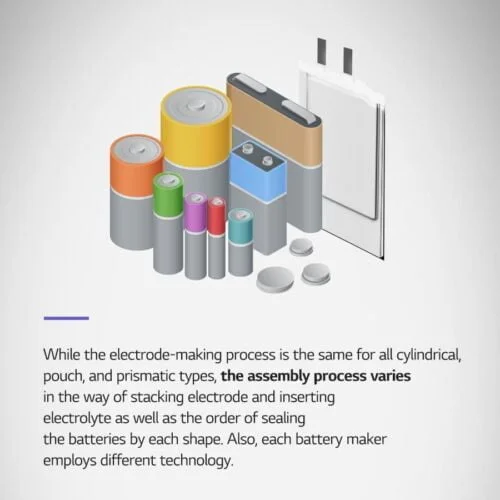
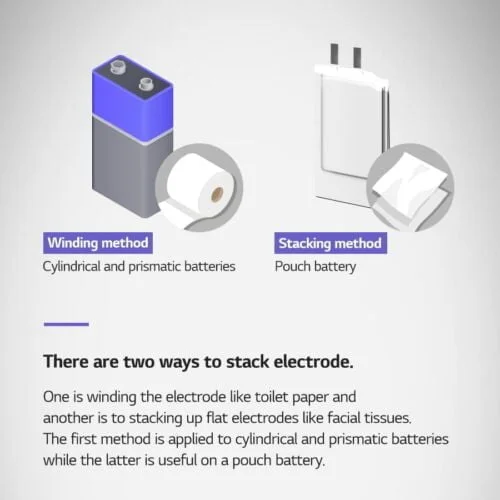
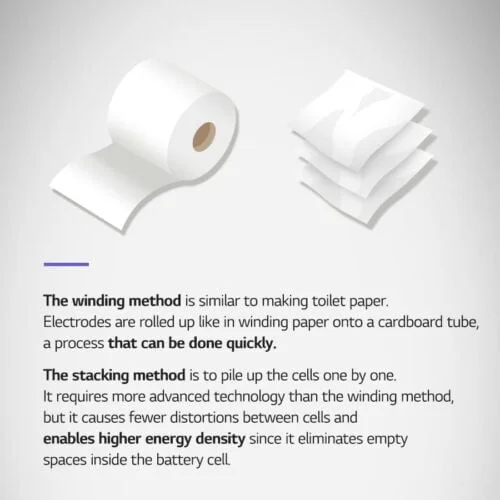
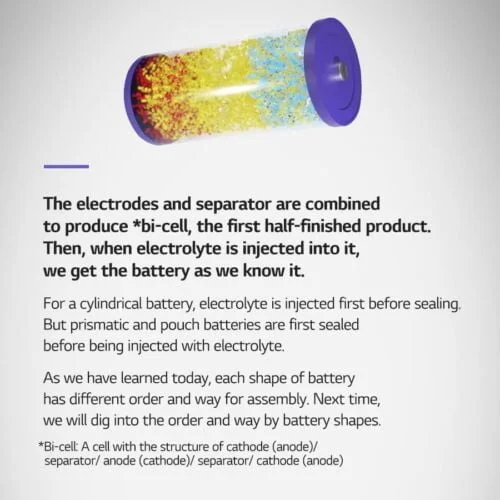
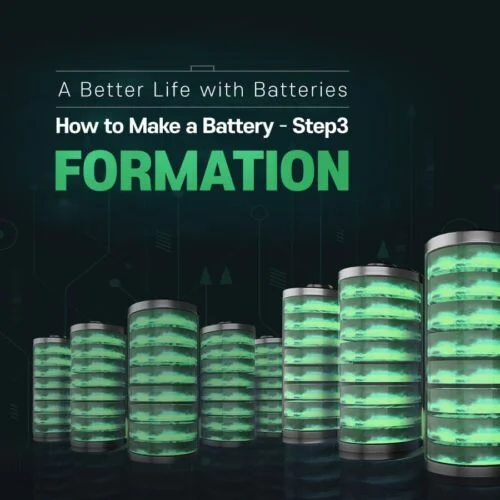
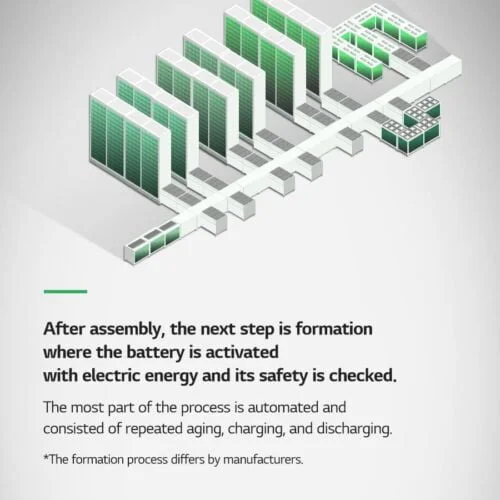
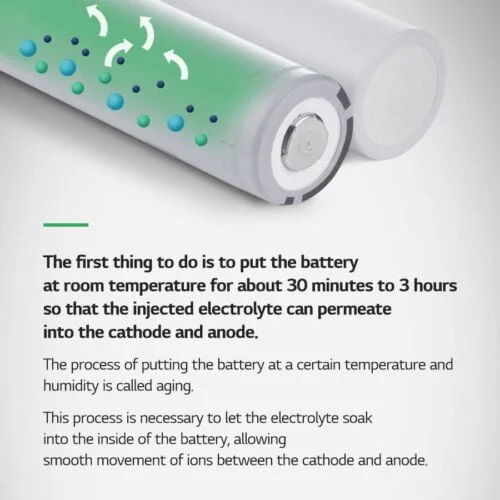
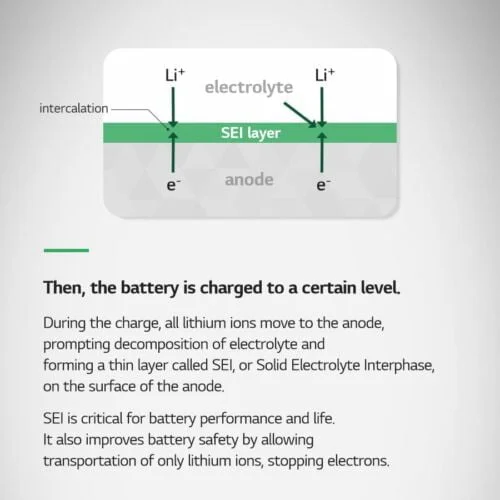
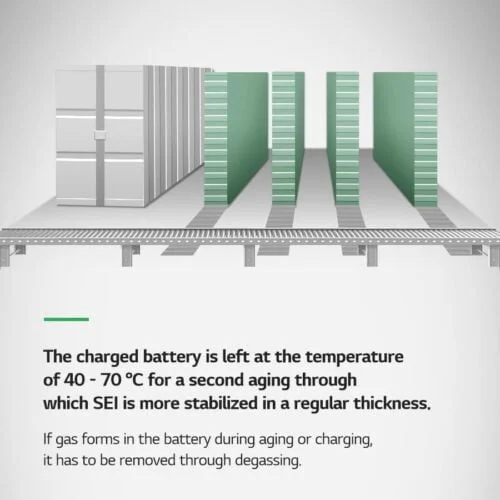
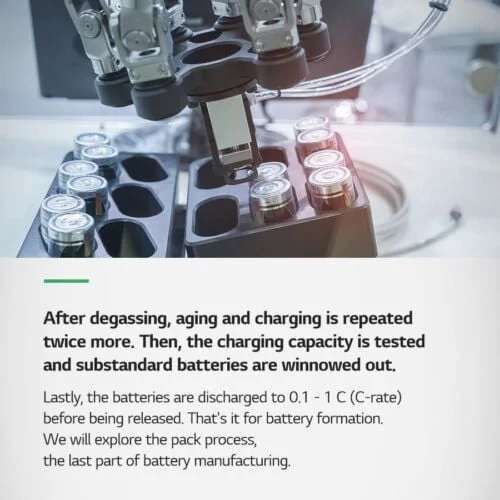
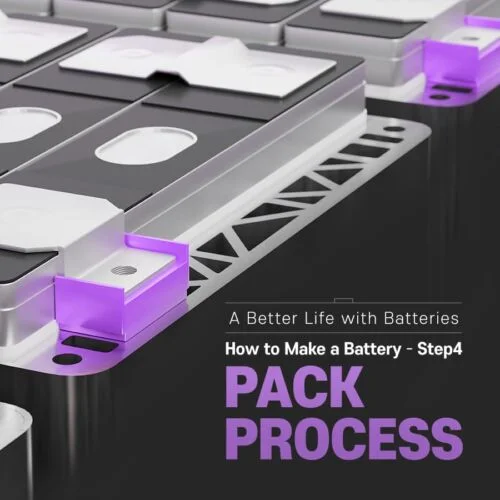
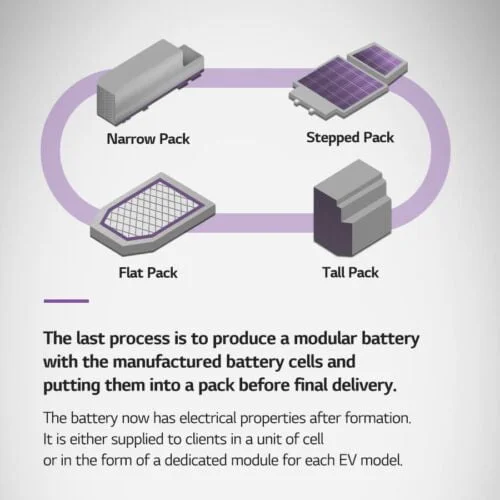
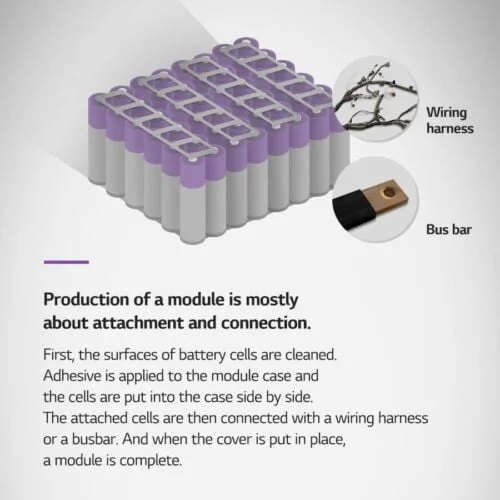
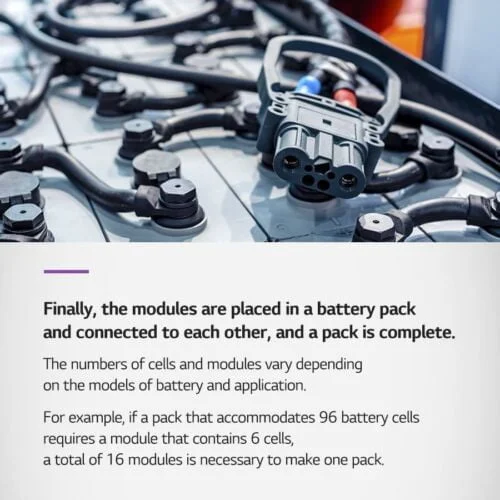
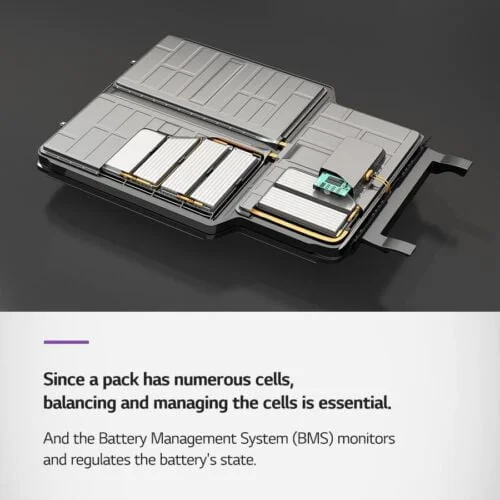
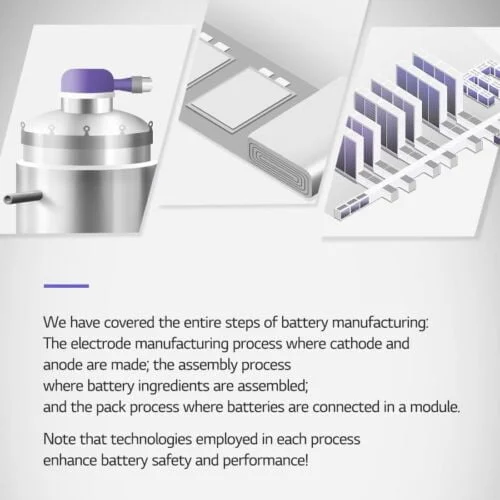
W całym procesie produkcyjnym, który jest w większości zautomatyzowany, ostatnie słowo ma człowiek – przynajmniej na razie. Przykładem może być kontrola jakości, gdzie zarówno na początku, jak i na końcu ścieżki, choć pracownicy wspierani są przez zautomatyzowane procesy, to ostatnie i decydujące zdanie mają technicy jakości.
Jak to działa?
Zasada działania baterii w samochodzie elektrycznym opiera się na reakcjach chemicznych. Przy anodzie powstaje nadmiar elektronów, a przy katodzie – niedobór. Różnica potencjałów określa napięcie elektryczne. Obrazując to najprościej, jak się da: w procesie ładowania, jony dodatnie (kationy) litu wędrują za pośrednictwem elektrolitu poprzez membranę do anody. Po podłączeniu odbiornika prądu – w tym przypadku jednostki elektrycznej napędzającej pojazd, nadmiarowe elektrony z anody wędrują przewodem do katody – płynie prąd zasilający. Kolejną ważną kwestią, która jest rozwijana w samochodach elektrycznych, to moc napięcia roboczego. Obecnie większość dostępnych modeli pracuje na instalacji 400V. Jednak już są dostępne modele, a ich liczba będzie się zwiększać z układami o napięciu 800V. Jaka jest różnica? Zwiększając napięcie można znacząco zwiększyć moc roboczą, zachowując stosunkowo zbliżoną pojemność akumulatora. Pozwala to również na zwiększenie mocy ładowania. Za przykład może posłużyć Porsche Taycan, który posiadając instalację 800V może ładować się z mocą do 270 kW.
LG rośnie w siłę
– Podstawą konkurencji jest nie tylko cena, ale i lepsza technologia czy dłuższe działanie baterii – powiedział nam Dyrektor ds. wsparcia biznesu LG Energy Solution Wrocław w Polsce Yong Girl Lee. Wskazał również, że jego firma kładzie nacisk na technologię, która pozwala na większą żywotność baterii i do inwestycji w lepszą jakość zachęca swoich klientów. Yong Girl Lee zwraca jednak uwagę, że pomimo tego, że sprzedaż baterii samochodowych LG Energy Solution rośnie, a produkcja trwa non stop, to jej rosnące koszty oraz coraz wyższe ceny energii znacznie podnoszą cenę finalnego produktu, co przekłada się na koszty nowego samochodu. Zauważa, że oczekiwana jest pomoc państwa w postaci mechanizmów zabezpieczających przedsiębiorstwa przed podwyżkami.
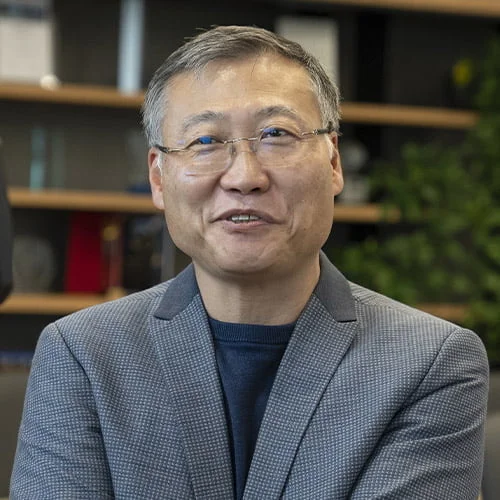
Z udostępnionych przez LG Energy Solution informacji wynika, że na dzień 26 października 2022 r., spółka może pochwalić się wzrostem rok do roku o 89,9 proc. i zyskiem operacyjnym na poziomie 522 mld KRW (jeden won południowokoreański to 0,0007 dolara amerykańskiego). Fabryka nie zamierza zwalniać tempa i przygotowuje się na dalszy rozwój, będąc już dzisiaj jednym z największych inwestorów i pracodawców na Dolnym Śląsku. W zakładzie w Biskupicach Podgórnych zatrudnieni są najlepsi inżynierowie oraz specjaliści, którzy pracują nad bateriami dla największych koncernów samochodowych na świecie. Po rozbudowie fabryki i osiągnięciu docelowej mocy produkcyjnej 115 GWh firma będzie dostarczała baterie do ponad miliona aut elektrycznych rocznie. Aby osiągać cele, spółka stale poszukuje najzdolniejszych ekspertów i inżynierów.
Kierunek rozwój
Zgodnie z wizją ESG (ang. Environmental, Social and Corporate Governance – środowisko naturalne, społeczeństwo i ład korporacyjny) „We CHARGE toward a better future”, LG Energy Solution Wrocław dąży do bycia firmą coraz bardziej przyjazną środowisku, wypełnia obowiązki społeczne i kształtuje zrównoważoną przyszłość – globalnie i lokalnie. Stawia klimat na pierwszym miejscu i kształtuje odpowiedzialne postawy wśród zespołu m.in. promując elektromobilność i tym samym zachęcając najlepszych ekspertów do dołączenia do wspierającego klimat biznesu. Każdy z pracowników może bezpłatnie wypożyczać elektryczne auta na weekend. Gigantyczna fabryka jest także zasilana w 100 proc. energią z odnawialnych źródeł energii.
Jak podkreśla kierownictwo firmy, produkcja baterii stanowi jedno z ogniw sektora. Rozwijać musi się również technologia recyklingu baterii.
– Recycling pozwala na ponowne wykorzystanie niemal wszystkich surowców użytych do produkcji baterii, co daje pewność, że ta gałąź biznesu będzie się prężnie rozwijać – podkreślił dyrektor Yong Girl Lee. Z informacji jakie udało się uzyskać od przedstawicieli spółki, zakład recyklingu będzie powstawał w niedalekiej odległości od zakładów produkcyjnych, ale nie na terenie LG Energy Solution Wrocław.
– Innowacyjność w takich obszarach jak recykling, sensoryka termiczna, BMS oraz software, musi być rozwijana na równi z mocami wytwórczymi, a być może nawet bardziej – uważa Aleksander Rajch, Director Of External Affairs w Polskim Stowarzyszeniu Paliw Alternatywnych.