Fakt 1 – recykling, to tylko jedno z wielu bateryjnych wyzwań
Rozwój technologii magazynowania energii elektrycznej (technologie bateryjne) i rozwój w zakresie produkcji baterii to strategiczne sektory dla Europy w kontekście przejścia na czystą energię. Nie bez znaczenia jest także udział krajów UE w globalnym rynku produkcji baterii (w którym aktualnie przodują Chiny) i wpływ na cały sektor motoryzacyjny w Europie.
Gospodarka i biznes są ważne, ale to nie wszystko. W UE transport odpowiada za około 25% emisji gazów cieplarnianych i jest jedną z głównych przyczyn zanieczyszczenia powietrza w miastach. To nie jest reguła, bo np. jeszcze kilka lat temu w Krakowie to nie transport, ale emisja z domowych pieców odpowiadała za większość zanieczyszczeń w powietrzu. Jednak bez wątpliwości, upowszechnienie pojazdów elektrycznych zmniejszy emisję gazów cieplarnianych i szkodliwych emisji z transportu drogowego i dodatkowo zmniejszy “zanieczyszczenie miast hałasem”.
Unijni urzędnicy zakładają, że w UE silny wzrost elektryfikacji samochodów osobowych, dostawczych i autobusów nastąpi w latach 2025–2030 (w transporcie ciężarowym kilka lat później). Wynika to głównie z prawodawstwa UE ustalającego normy emisji CO 2 dla producentów pojazdów, ale także przez prawodawstwo UE określające minimalne cele państw członkowskich w zakresie zamówień publicznych na ekologicznie czyste pojazdy. Tak więc szczyt wyzwania recyklingu baterii dopiero przed nami, bo według szacunków Światowego Forum Ekonomicznego istnieje potrzeba 19-krotnego zwiększenia światowej produkcji baterii, aby przyspieszyć przejście na gospodarkę niskoemisyjną.

Inicjatywy UE są ukierunkowane na unowocześnienie ram legislacyjnych dotyczących baterii. To integralna część Zielonego Ładu (European Green Deal), strategii UE na rzecz wzrostu, której celem jest przekształcenie UE w nowoczesną i konkurencyjną gospodarkę, w której m.in do 2050 roku nie będzie emisji netto gazów cieplarnianych.
Opierają się one na nowym planie działania dotyczącym gospodarki o obiegu zamkniętym, nowej strategii przemysłowej dla Europy, strategii na rzecz zrównoważonej i inteligentnej mobilności, której celem jest zapewnienie redukcji emisji gazów cieplarnianych związanych z transportem o 90% do 2050 roku oraz (a może przede wszystkim) na strategicznym planie działania w sprawie baterii.
Tytułowy recykling baterii jest tylko jednym z elementów całego systemu, bo wyzwania związane z bateriami znacznie wykraczają poza kwestię ich utylizacji i recyklingu. Według rozporządzenia Komisji i Rady Europejskiej z 2020 roku (uchylającego pierwszy obszerny dokument z 2018 i kolejny z 2019 roku), są trzy obszary (grupy) wyzwań związanych z bateriami:
“Pierwsza grupa wiąże się z brakiem warunków ramowych zachęcających do inwestowania w moce produkcyjne zrównoważonych baterii. Problemy te są powiązane z nieefektywnym funkcjonowaniem jednolitego rynku oraz brakiem wystarczająco równych warunków działania ze względu na rozbieżne ramy regulacyjne na rynku wewnętrznym. (…)”
“Druga grupa problemów wiąże się z nieoptymalnym funkcjonowaniem rynków recyklingu i niedostatecznie zamkniętymi obiegami materiałowymi, co ogranicza potencjał UE w zakresie ograniczania ryzyka dostaw surowców..(…).”
“Trzecia grupa problemów dotyczy zagrożeń społecznych i środowiskowych, które obecnie nie są objęte unijnym prawem ochrony środowiska. Problemy te obejmują: brak przejrzystości w zakresie pozyskiwania surowców; substancje niebezpieczne oraz niewykorzystany potencjał równoważenia wpływu cykli życia baterii na środowisko.”
Łańcuch wartości w sektorze baterii powinien stanowić obieg jak najbardziej zamknięty. Składa się on z kilku etapów: od wydobycia i przetwórstwa surowców przez produkcję elementów akumulatorów i samych ogniw baterii oraz ich demontaż i recykling (lub nadanie “drugiego życia” baterii trakcyjnej).

Fakt 2 – UE precyzuje przepisy i stawia jasne cele – zamknięty obieg
Najnowsze przepisy dotyczące całego cyklu życia zostały przegłosowane 10 lipca i zaktualizowane 17 sierpnia 2023 roku. Regulacje te mają służyć promowaniu gospodarki o wspomnianym wyżej obiegu zamkniętym. Obejmują one zatem wymogi co do postępowania z zużytymi bateriami, w tym cele i obowiązki w zakresie ich zbiórki, cele w zakresie odzysku materiałów i obowiązki dotyczące rozszerzonej odpowiedzialności producenta.
Rozporządzenie określa obowiązujące producentów cele w zakresie odzyskiwania zużytych baterii przenośnych (63% do końca 2027 r. i 73% do końca 2030 r.) i wprowadza specjalny cel dotyczący odzyskiwania zużytych baterii z lekkich środków transportu (51% do końca 2028 r. i 61% do końca 2031 r.).
Ustala również cel dotyczący odzyskiwania litu – na poziomie 50% do końca 2027 r. i 80% do końca 2031 r. Przy czym zakłada się, że wartości te mogą zostać zmienione w zależności od postępów rynkowych i technologicznych i dostępności surowców.
Rozporządzenie przewiduje także obowiązkowe minimalne poziomy zawartości materiałów z recyklingu w odniesieniu do baterii przemysłowych oraz akumulatorów pojazdów i maszyn. Docelowe poziomy wstępnie wynoszą 16% kobaltu, 85% ołowiu, 6% litu i 6% niklu. Baterie będą musiały posiadać dokumentację poświadczającą zawartość materiałów z recyklingu.
Do końca 2025 r. wydajność recyklingu ma wynieść 80% dla baterii niklowo-kadmowych i 50% dla innych zużytych baterii.
Do 2027 r. użytkownicy końcowi powinni mieć możliwość łatwego demontażu i wymiany baterii przenośnych wmontowanych do urządzeń. Termin dość odległy, ale dzięki temu zapewni wytwórcom wystarczająco dużo czasu na dostosowanie produktów do tego wymogu. Przepis ma duże znaczenie dla klientów, bo baterie z lekkich środków transportu będzie można szybko, łatwo (a przez to relatywnie tanio) wymienić.
Bateryjny paszport
W rozporządzeniu wprowadzano wymogi informacyjne i wymogi dotyczące etykietowania, m.in. w odniesieniu do komponentów baterii i zawartości materiałów z odzysku, a także „paszport” baterii wraz z kod QR informujący m.in o lokalizacjach punktów w łańcuchu dostaw, pochodzeniu pierwiastków, śladzie węglowym, ale zawierający również dane w zakresie praw człowieka i indeksie wykorzystania pracy dzieci. Aby zapewnić państwom członkowskim i podmiotom gospodarczym wystarczająco dużo czasu na przygotowanie, wymogi dotyczące etykietowania zaczną obowiązywać najpóźniej w 2026 r, a kod QR – w 2027 r.

Fakt 3 – żywotność akumulatorów zależy od wielu czynników
Kwestia żywotności baterii samochodów elektrycznych to osobna dziedzina nauki, ale w dużym uproszczeniu zależy od zastosowanej technologii bateryjnej, ładowania i warunków użytkowania. W obszarze technologii bateryjnych przyszłością są baterie ze stałym elektrolitem, które różnią się wykorzystaną chemią od niemal wszystkich obecnie użytkowanych baterii trakcyjnych zbudowanych na bazie litu. Stosowane są dwie podstawowe technologie baterii litowo-jonowych, które różnią się m.in żywotnością – akumulatory NMC i LFP.
W bardzo dużym uproszczeniu baterie LFP osiągają od 3000 do 6000 cykli ładowania, jeśli są używane i serwisowane prawidłowo, natomiast baterie NMC zachowują żywotność niższą o około 30-60%. Co więcej, stopień samorozładowania akumulatorów LFP wynosi ok. 3% miesięcznie, ale akumulatory NMC ulegają samorozładowaniu w tempie ok. 4% miesięcznie. W obszarze technologii nie bez znaczenia jest też kwestia oprogramowania pojazdu i ładowarki pokładowej (w przypadku ładowania AC) i oprogramowania ładowarki DC, która komunikuje się z samochodem za pomocą protokołu OCPP. Wpływ na żywotność ma również technologia ogrzewania i chłodzenia baterii.
Tutaj dochodzimy do kwestii czynników zewnętrznych. Akumulatory trakcyjne pracują optymalnie w pewnym oknie temperaturowym, dlatego skrajnie niskie lub skrajnie wysokie temperatury zewnętrzne mocno wpływają na żywotność całego pakietu. Osobną kwestią jest sposób użytkowania i w szczególności głębokie rozładowanie przez dłuższy czas lub regularne głębokie rozładowania mogą skrócić trwałość baterii.

Fakt 4 – żywotność baterii jest wyższa niż zakładano
Jeszcze w 2013 roku, czyli na początku procesu wymiany flot miejskich przewoźników na elektryczne, ówczesny rzecznik prasowy firmy produkującej autobusy – Solaris Bus & Coach, Mateusz Figaszewski, publicznie głosił: “Dzisiaj możemy powiedzieć, że w ciągu „życia” autobusu na pewno raz trzeba będzie wymienić baterię”.
Jeszcze dekadę temu, nikt nie wiedział, jaka będzie realna żywotność pakietów baterii i dlatego bardzo konserwatywnie zakładano, że akumulatory po 5-6 latach będą wymagały wymiany na nowe. Dzisiaj, po ponad 10 latach użytkowania wiemy, że te prognozy były bardzo asekuracyjne i mocno niedoszacowane. Realna żywotność baterii to około 10-13 lat, czyli szacunkowo tyle, ile wynosi zakładany okres eksploatacji całego pojazdu. Baterie, które już zakończyły pracę w autobusach elektrycznych nadal posiadają około 70 – 80% swojej pierwotnej pojemności i są całkowicie sprawne.

Fakt 5 – pierwiastki ziem rzadkich to złoto naszych czasów (aluminium i stal również)
Przedmiotem recyklingu są przede wszystkim surowce krytyczne, często pozyskiwane w dyskusyjnych warunkach (stąd w paszportach baterii kwestia wykorzystywania dzieci do pracy). Typowy akumulator trakcyjny o pojemności 50 kWh zawiera około czterech do ośmiu kilogramów litu, jedenaście kilogramów manganu, dwanaście kilogramów kobaltu i niklu oraz 33 kilogramy grafitu.
Zasadniczo, po wyprodukowaniu i w związku z użytkowaniem, cykl życia przebiega w trzech etapach: naprawa (jeśli to konieczne), ponowne użycie (tzw. “drugie życie”) i recykling. Zgodnie z nowym unijnym rozporządzeniem dotyczącym akumulatorów, w przyszłości wskaźnik recyklingu wyniesie 80 proc. (a od 2031 r. nawet 95 proc.). Obecnie odzyskowi poddawane są również aluminium, stal i tworzywa sztuczne, a w przyszłości recyklingowi będą podlegać także inne materiały.

Fakt 6 – drugie życie nie gorsze od pierwszego
Zanim częściowo zdegradowane akumulatory samochodowe, których pojemność spadła po wielu cyklach ładowania, zostaną poddane recyklingowi, można im dać drugie życie w pracy stacjonarnej np. w magazynach energii. Przyjmuje się, że po dziesięciu latach eksploatacji, akumulatory nadal są w pełni zdatne do użytku, mimo iż mają ok 70-80 procent pierwotnej pojemności. W przypadku racjonalnej eksploatacji podczas “drugiego życia” można ich używać przez kolejne dziesięć do dwunastu lat, dlatego recykling baterii rozpoczyna się dopiero po ok. 20 latach użytkowania.

Fakt 7 – trzecie życie odzyskanych pierwiastków zaczyna się od pełnego rozładowania
Jesteśmy jeszcze wiele lat od szczytu napływu zużytych baterii po etapie “drugiego życia” ale firmy już się do tego przygotowują. Nic dziwnego: według Instytutu Fraunhofera ds. Badań nad Systemami i Innowacjami infrastruktura niezbędna do recyklingu wymaga inwestycji o wartości ponad sześciu miliardów euro do roku 2040. Przed recyklingiem konieczne jest całkowite i zupełne rozładowanie akumulatorów i do tego etapu potrzebne są odpowiednie rozwiązania.Na przykład spółka zależna Bosch – Rexroth zaprezentowała technologię, w której automatyczne rozładowywanie ogniw akumulatorowych ma na celu zwiększenie efektywności i bezpieczeństwa recyklingu. W przedsiębiorstwie Battery Lifecycle Company w Magdeburgu budowany jest zakład pilotażowy, którego zadaniem jest ekspresowe usunięcie resztek energii z akumulatorów.
Osiem akumulatorów litowo-jonowych z samochodów elektrycznych można automatycznie rozładować w czasie krótszym niż 15 minut. System nie tylko rozpoznaje różne konstrukcje akumulatorów, ale może także zapobiegać zwarciom i pożarom. Największa zaleta: dalsza obróbka może odbywać się bez napięcia. W przypadku zwykłego procesu ręcznego całkowite rozładowanie akumulatorów zajmuje do 24 godzin.
Dalszy proces recyklingu jest złożony: po ręcznym demontażu systemów akumulatorów następuje sortowanie i rozdrabnianie. Poszczególne składniki oddzielane są za pomocą sit i magnesów. Tzw. czarną masę można otrzymać w wyniku reakcji chemicznych, podczas których rozpuszcza się substancje w roztworach wodnych poprzez dodanie środków chemicznych (hydrometalurgia). “Czarna masa” zawiera pierwiastki takie jak grafit, mangan, nikiel, kobalt i lit.
Fakt 8 – recykling to skomplikowana technologia
Obecnie najpowszechniejszym podejściem jest recykling termiczny. Uprzednio rozdrobnione akumulatory są poddawane procesom chemicznym i termicznym. Tworzy się ciemna, lepka masa, którą słusznie nazywa się czarną masą. Aby wykorzystać różne temperatury wrzenia składników, wymagane są temperatury do 1450 stopni. Innymi słowy: wygrzewana jest masa składająca się ze składników kobaltu, niklu, litu i miedzi. Surowce są następnie dalej rozdzielane w różnych procesach.
Według podążającej tą drogą firmy recyklingowej Umicore, w procesie pirometalurgicznym ponad 95 procent użytego kobaltu, miedzi i niklu udaje się odzyskać. Surowce są następnie oddzielane za pomocą procesów mechanicznych i chemicznych.
Aby uczynić recykling jeszcze bardziej przyjaznym dla środowiska, istnieją dwa inne podejścia, które są jednak wciąż rozwijane. Uniwersytet Rice w Houston w Teksasie pracuje nad systemem ogrzewania Flash Joule. W tym procesie czarna masa jest podgrzewana do 1800 stopni Celsjusza w ciągu kilku sekund, podczas gdy surowce są rozpuszczane za pomocą kwasu. Proces ten powinien pozwolić na recykling 98 procent surowców.
Naukowcy z Uniwersytetu Chalmers w Szwecji osiągnęli podobny poziom recyklingu, eliminując użycie kwasów nieorganicznych. Zastosowanie kwasu szczawiowego, substancji z królestwa roślin występującej na przykład w szpinaku, pozwala na lepszą efektywność energetyczną i odzysk prawie wszystkich surowców: aluminium jest w całości poddawane recyklingowi, lit w 98%. Minimalizowane są także straty niklu, kobaltu i manganu.
Fakt 9 – różne drogi do jednego celu
Oprócz producentów akumulatorów i firm zajmujących się recyklingiem, wyzwaniu przyglądają się także sami producenci samochodów. Oto przegląd wysiłków na rzecz recyklingu akumulatorów samochodów elektrycznych:
Stellantis
Koncern Stellantis nawiązał współpracę z firmą recyklingową Orano w celu recyklingu na szeroką skalę zużytych akumulatorów z samochodów elektrycznych. Odpowiednie gigafabryki mają powstać w Europie i Ameryce Północnej. Jeden z tych zakładów ma być zlokalizowany w istniejącej lokalizacji Orano w Dunkierce. Francuskie miasto dąży do osiągnięcia wskaźnika recyklingu akumulatorów litowo-jonowych na poziomie ponad 90 procent przy użyciu najnowszych procesów hydrometalurgicznych. Testowane są także nowe materiały na katody.
Volkswagen
Volkswagen otworzył zakład recyklingu akumulatorów w swojej lokalizacji w Salzgitter (Dolna Saksonia). Tutaj w obiegu zamkniętym mają być odzyskiwane cenne surowce, takie jak lit, nikiel, mangan i kobalt. Nawet w przypadku aluminium, miedzi i tworzyw sztucznych wskaźnik recyklingu powinien w perspektywie średnioterminowej przekroczyć 90%.
W pierwszym etapie zakład w Salzgitter ma przetwarzać do 3600 systemów akumulatorowych rocznie, co odpowiada około 1500 tonom materiału. System można później skalować do większych ilości przy użyciu zoptymalizowanych procesów.
„W ten sposób Volkswagen Group Components robi kolejny krok w swojej zrównoważonej, kompleksowej odpowiedzialności za akumulatory jako kluczowy element elektromobilności” – powiedział członek zarządu Volkswagena Thomas Schmall.
Mercedes
Mercedes buduje własną fabrykę recyklingu akumulatorów w Kuppenheim na południe od Karlsruhe, opartą na hydrometalurgii o rocznej wydajności 2500 ton. Firma planuje wraz z partnerami z branży zaawansowanych technologii stworzyć zamknięty obieg recyklingu w zakresie recyklingu akumulatorów również w Chinach i USA.

– Zrównoważony recykling akumulatorów jest ważnym czynnikiem – na całym świecie. Dzięki naszej nowej fabryce recyklingu w Kuppenheim zwiększamy wskaźnik recyklingu do ponad 96 procent i konsekwentnie poszerzamy nasze kompetencje w obszarze tworzenie wartości baterii – powiedział Dyrektor produkcji Mercedesa, Jörg Burzer.
Odzyskane materiały trafiają do recyklingu i wykorzystywane są do produkcji ponad 50 000 modułów akumulatorowych do nowych modeli Mercedes serii EQ.
BMW
Koncern z Monachium obsługuje już system magazynowania w fabryce w Lipsku składający się z 700 połączonych ze sobą akumulatorów z modeli i3, które buforują energię z turbin słonecznych i wiatrowych w drugim życiu do wykorzystania w produkcji. BMW chce jak najdłużej korzystać z drogiej technologii akumulatorów.
Chińska spółka joint venture BMW Brilliance Automotive ustanowiła zamknięty cykl ponownego wykorzystania podstawowych surowców do produkcji akumulatorów: niklu, litu i kobaltu. W pierwszym etapie akumulatory pochodzą z pojazdów rozwojowych i obiektów testowych. W dłuższej perspektywie podzespoły wycofanych pojazdów również powinny zostać poddane recyklingowi.

BMW Brilliance Automotive współpracuje z lokalną firmą zajmującą się recyklingiem, która demontuje zużyte baterie i odzyskuje surowce, nikiel, lit i kobalt z ogniw baterii. Uzyskane w ten sposób surowce wykorzystywane są następnie do produkcji nowych ogniw akumulatorowych dla BMW Group.
Jochen Goller, dyrektor BMW Group na region Chiny: „W przyszłości BMW Group będzie dalej rozwijać koncepcję recyklingu w Chinach, która nie tylko przyczynia się do ochrony środowiska, ale także skutecznie wspiera przejście na gospodarkę o niskiej emisji CO 2″
Audi
Każdy, kto choć raz był w Indiach, zna charakterystyczne trójkołowce, które dominują na ulicach większości metropolii. Do tej pory tuk-tuki z silnikami spalinowymi przemierzały ponad milionowe miasta, takie jak Bombaj, Delhi czy Chennai. Rząd chce jednak, aby to się wkrótce zmieniło, bo subkontynent indyjski chce w nadchodzących dekadach stopniowo przechodzić na energię elektryczną.

Audi wraz z niemiecko-indyjskim start-upem Nunam rozpoczęło wykorzystanie akumulatorów w tuk-tukach. W ramach eksperymentu modelowego elektryczne trójkołowce zasilane są zużytymi akumulatorami z elektrycznych pojazdów testowych.
„Wycofane z samochodów baterie są nadal niezwykle wydajne” – mówi Prodip Chatterjee, współzałożyciel Nunam. Dodaje: „Baterie drugiego życia, użyte we właściwych zastosowaniach, mogą mieć ogromny wpływ, pomagając ludziom w trudnych sytuacjach życiowych osiągnąć dochód i niezależność ekonomiczną – w sposób zrównoważony”. Trójkołowce, które są już napędzane elektrycznie, napędzane są głównie akumulatorami kwasowo-ołowiowymi, które mają krótką żywotność.
Jaguar Land Rover
Jaguar Land Rover wraz z firmą energetyczną Pramac opracował system magazynowania energii, który wykorzystuje zdemontowane akumulatory do zapewnienia zasilania. W pierwszym etapie współpracy mobilny system przechowywania ESS wykorzystuje ogniwa litowo-jonowe z prototypów i przedprodukcyjnych modeli Jaguara I-Pace .
Cel: System magazynowania przeznaczony jest do dostarczania energii tam, gdzie dostęp do publicznej sieci elektroenergetycznej jest ograniczony lub w ogóle nie istnieje. Mobilny system magazynowania ma obecnie pojemność do 125 kWh – to więcej niż wystarczająco do naładowania samochodu elektrycznego lub zasilenia domu jednorodzinnego przez tydzień. Akumulator ESS działający poza siecią będzie w przyszłości używany także w Jaguar Land Rover Experience Center w Johannesburgu w Republice Południowej Afryki do zasilania zmiennofazowego zasilania z sieci publicznej.
Fakt 10 – Recykling to szansa na rozwój i duże pieniądze
W Europie sprzedaje się ponad 12 milionów samochodów rocznie, a według szacunków, do 2030 roku udział EV w całkowitej sprzedaży nowych samochodów w Europie wyniesie 24 %. To oznacza, że za kilka-kilkanaście lat rynek recyklingu będzie regularnie zasilany milionami baterii z drogocennymi pierwiastkami do odzyskania. Póki co kwestia recyklingu jest niszowa, ale Europa staje przed dużą szansą biznesową, bo opracowanie wydajnych technologii i odpowiednich przepisów może dać tysiące miejsc pracy. Dodatkowo, nie bez znaczenia jest kwestia niezależności krajów EU od zakupu pierwiastków w innych częściach świata. Im wyższy poziom odzysku minerałów, tym wyższe bezpieczeństwo globalnego łańcucha dostaw.
Podsumowanie
Wraz ze zmianą przepisów dotyczących recyklingu baterii kroczy rozwój technologii. Cieszy fakt, że koncerny samochodowe wykorzystują potencjał finansowy i technologiczny do inwestycji w technologie odzyskiwania wartości ze zużytych baterii. Recykling na poziomie 96% osiągany przez nowy zakład Mercedesa daje powiew optymizmu na uzyskiwanie wysokiej efektywności w masowych procesach. Wskaźniki recyklingu na poziomie ponad 90%, realizowane przez inne koncerny motoryzacyjne z Europy są dowodem, że plany uzyskania “gospodarki obiegu zamkniętego” nie są tylko kolejnym wymysłem “unijnej biurokracji” jak niektórzy starają się przedstawiać, lecz rzeczywistością, która właśnie się dzieje. Polska jest europejskim centrum produkcji akumulatorów i również ma szansę stać się centrum odzyskiwania pierwiastków ze zużytych akumulatorów. To ogromna szansa dla biznesu i całej gospodarki w Polsce i Europie.
elektromobilni.pl
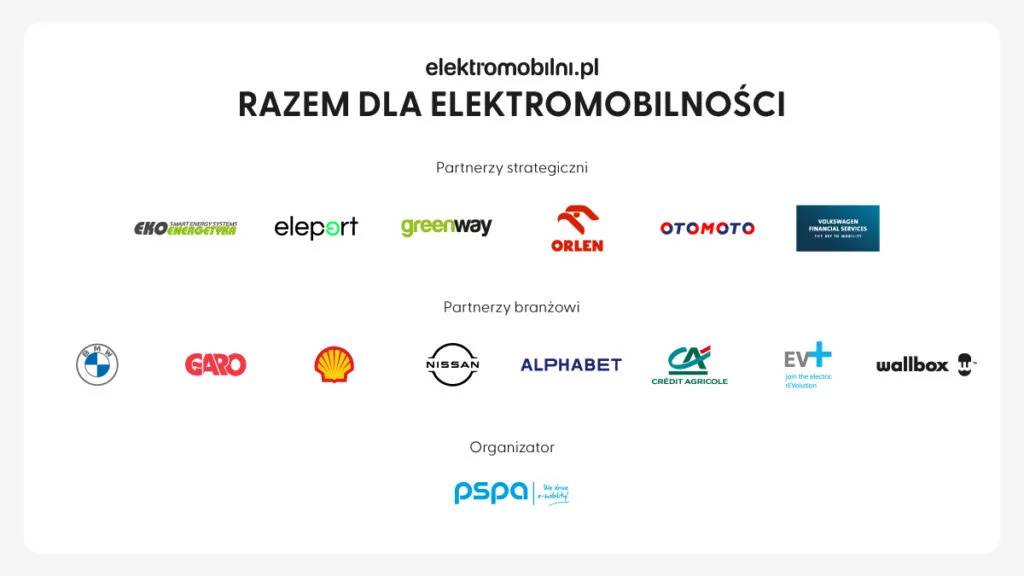