W Gruenheide pod Berlinem działa fabryka Tesli. Jej huczne otwarcie poprowadził Elon Musk wraz kanclerzem Olafem Scholzem i ministrem gospodarki Robertem Habeckiem. Sama budowa trwała dwa lata. Nie oznacza to jednak, że prace budowlane ustały. W 24 miesiące udało się stworzyć linie produkcyjne oraz wszystkie niezbędne budynki. Kolejne prace budowalno-wykończeniowe nadal trwają. Po ich zakończeniu osiągnięte zostanie docelowe zatrudnienie 12 tys. osób oraz produkcja do 500 tysięcy pojazdów rocznie.

Innowacyjność i robotyzacja
Jak mogliśmy wielokrotnie usłyszeć ze słów Elona Muska, Gigafabryka w Berlinie miał być i jest (podobno) nowoczesną fabryką. Jednak do tej pory mogliśmy opierać się wyłącznie na potwierdzeniach m.in. poprzez nagrane wideo. Teraz sprawdzamy to sami!
Trzeba przyznać, że już od samego początku robi ona nie lada wrażenie. Przed budynkiem głównym powstała sieć infrastruktury ładowania pojazdów elektrycznych. Jest to jednak nic w porównaniu z tym co mogliśmy zobaczyć na halach produkcyjnych.

400 robotów dzień w dzień wykonuje mosiężną pracę, by tygodniowo mogło z taśmy produkcyjnej zjechać 5000 pojazdów, a w skali roku ćwierć miliona. Oznacza to, że na jeden pojazd na razie przeznaczane jest około 10 roboczogodzin. Na jednej z linii, podczas jednej zmiany, czuwa 300 pracowników.
Bateryjna rewolucja
Interesującą jest również linia małżeńska, gdzie powstaje serce samochodu elektrycznego, czyli akumulator oraz silnik. W tym miejscu warto zaznaczyć, jak rozwijano w Tesli ogniwa (moce produkcyjne wynoszą na razie 50 GhW/A).
Rozwój baterii w Tesli nie ustaje. Na początku do Modeli S i X oferowano produkt 1685. Następnie pojawiły się lepsze i bardziej doskonałe ogniwa mogące gromadzić do 1,5-raza więcej energii (2170). Zaoferowano jest w Modelach 3 i Y. Teraz te samochody otrzymały nowy pakiet gromadzący 5-razy więcej energii (4680).
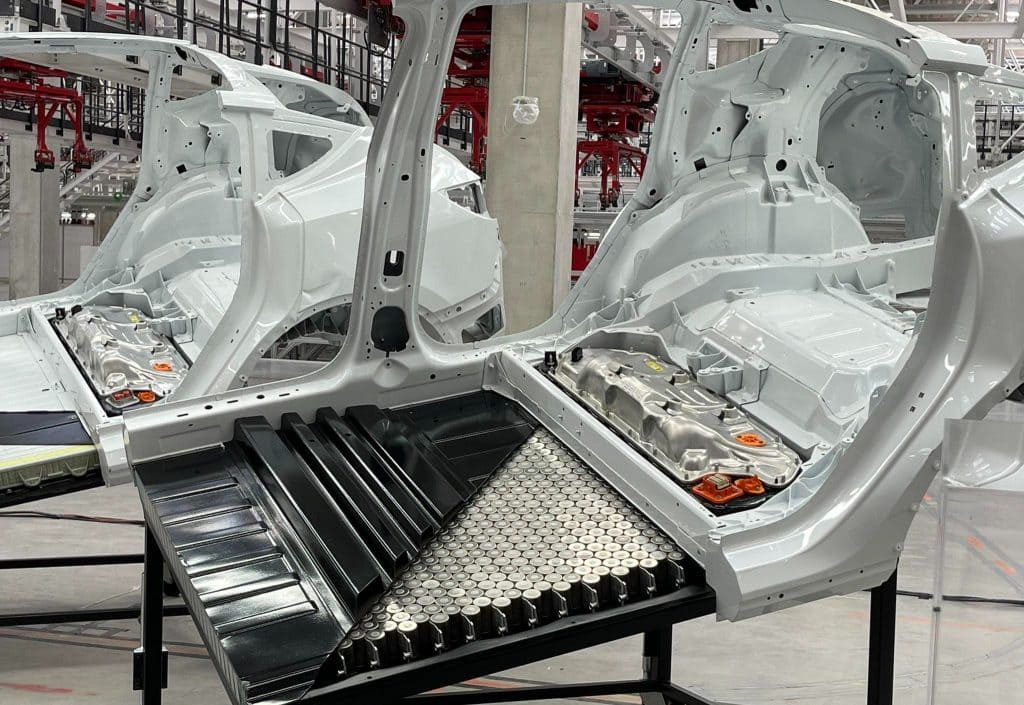
Mimo mocnej pierwszej pozycji na globalnym rynku, amerykański producent nie spoczywa na laurach i próbuje jeszcze bardziej wyprzedzić konkurencję. Dobrym tego przykładem jest fakt, że w bateriach od Tesli nie ma modułów. W zamian zastosowano pakiet strukturalny, który jest wystarczająco sztywny, aby wytrzymać wszystkie działające siły i naprężenia. W efekcie jest o około 370 mniej części, a dodatkowo uzyskano o 14% większy zasięg i o 10% zmniejszono masę zestawu.
Pod dużym naciskiem
Choć brzmi to imponująco – a nie są to pełne moce przerobowe – to jeszcze bardziej interesującą częścią samego zakładu jest tłocznia. To właśnie tam prasa pod naciskiem 2500 ton produkują 2 elementy w 4 sekundy. Drugie tego typu urządzenie ma przydomek „giga”. Nie jest jednak związane z nazwą fabryki, ale faktem, że nacisk przez nią wytwarzany to bagatela 6100 ton. W efekcie w tej części fabryki są 4 prasy, a docelowo ma być ich 8.
Cała produkcja pojazdów elektrycznych nie może się odbywać bez ekologicznego wątku. Dlatego jasno zostaliśmy poinformowani, że odpady powstałe z procesu tworzenia pojazdów są w pełni poddawane recyklingowi. Dodatkowo Gigafabryka w Berlinie jest tworzony jako zakład docelowo neutralny emisyjnie. Dlatego już w tym momencie zastosowane są pompy ciepła i fotowoltaika. W efekcie obiekt będzie potrzebował o połowę mniej energii niż jest obecnie wykorzystywana. Co więcej Gigafabryka w Berlinie zużywa najmniej wody ze wszystkich producentów w przeliczeniu na pojazd (1,8 m3).

Polski wątek
Biorąc pod uwagę lokalizację zakładów Tesli, nie sposób pominąć polskiego wątku. Otóż obecnie pracuje tam wielu Polaków – na maj 2023 r. jest to blisko 20% załogi. Głównie zajmują się obsługą materiałów do budowy akumulatora dla Modelu Y. Ten odsetek może się zwiększyć, gdyż rekrutacja nadal trwa w Sulechowie, Gorzowie Wielkopolskim, Nowym Tomyślu czy Poznaniu.
Pracodawca rozumiejąc potrzeby osób dojeżdżających zorganizował autobusy dojeżdżające do miejsca pracy, m.in. z takich miejscowości jak Kostrzyn czy Słubice. Organizuje również kursy języka niemieckiego. Z kolei zagraniczni managerowie szkolą się w języku polskim.
Przechodząc na zeroemisyjność
Tesla jest producentem, który wszystko chce wytwarzać (albo przynajmniej to co może) własnymi siłami. Z tego względu w Gigafabryka w Berlinie powstaje nie tylko pojazd, ale też fotele i akumulatory. W efekcie powstaje produkt finalny, który nie tylko jest najlepiej sprzedającym się elektrykiem w ujęciu globalnym, ale też kluczem do uniezależnienia się m.in. do uniezależnienia się od dostaw paliw kopalnych, które rocznie w sektorze transportu pochłaniają 70 miliardów euro. Przechodząc na zeroemisyjność można by zaoszczędzić łącznie 200 miliardów rocznie.

Odwiedziny w Gigafabryka w Berlinie to przykład jak wygląda nowoczesny zakład wytwarzania pojazdów. nie ma co ukrywać pomysły wdrażane w ostatnim czasie przez Teslę, trafiają w gusta odbiorców. Mowa m.in. o próbie zmniejszenia kosztów produkcyjnych na rzecz tańszych samochodów, czy sam koncept samochodu połączonego z chmurą. Jest to coś czego świat chce. W efekcie inni producenci powinni uczyć się od Tesli jak powinno się podchodzić do kwestii pojazdów elektrycznych. Z kolei Tesla powinna wyciągnąć wnioski z precyzji i jakości samochodów sprzedawanych w Europie. Gdyby pod tym kątem się poprawiła to nie byłoby sensu kupować innych zeroemisyjnych aut niż te oferowane od amerykańskiego producenta z siedzibą główną w Austin, w stanie Teksas.
Autor: Aleksander Rajch