Samochody elektryczne nie emitują substancji szkodliwych w tym gazów cieplarnianych (m.in. CO2) podczas jazdy. Właśnie z tego powodu bywają określane mianem przyjaznych dla środowiska. Czy tak jest w istocie? Badania pokazują, że sumaryczny ślad węglowy zostawiane przez pojazdy BEV jest niższy niż w przypadku modeli spalinowych – nawet jeśli bierzemy pod uwagę emisję powodowaną przez proces produkcji auta i przez wytwarzanie energii potrzebnej do jego ładowania, również w krajach, które mają mało „zielony” miks energetyczny, czyli np. w Polsce.
Argumentem często podnoszonym przez przeciwników elektromobilności jest rzekoma krótka żywotność baterii w autach EV i fakt, że do ich produkcji używa się metali ziem rzadkich, występujących głównie w krajach Trzeciego Świata. Nie da się ukryć, że – mimo wysiłków producentów i ograniczania udziału kobaltu, niklu czy litu – rzeczywiście takie surowce są wykorzystywane. Na szczęście już teraz stosuje się recykling baterii. W najbliższym czasie będzie on przybierał na znaczeniu, stanie się efektywniejszy i prostszy.
Po co recyklinguje się baterie?
Wbrew obiegowym opiniom opartym na obserwacji baterii ze sprzętu elektronicznego codziennego użytku – czyli np. telefonów komórkowych – zużycie akumulatorów samochodowych i spadek ich wydajności nie jest ani tak szybkie, ani tak potężne, jak mogłoby się wydawać. Jak szacują specjaliści, akumulatory aut obecnie jeżdżących po drogach bez problemu posłużą nawet przez 15-20 lat, a prawdopodobnie także dłużej. Producenci zwykle oferują na baterie gwarancje trwające 8 lat. Auto po jej upływie wciąż powinno jednak zapewniać zadowalający zasięg.
Co jednak dzieje się z akumulatorem, gdy nie może już służyć w samochodzie? Należy odzyskać z niego tak wiele cennych surowców, jak to możliwe. Jak podaje Futuretracker.com, w 2020 r. żywotność około 550 000 akumulatorów z pojazdów elektrycznych dobiegła końca.
Recykling akumulatorów robi się więc zarówno ze względu na środowisko, jak i z powodów finansowych. Korzystniej jest odzyskać surowce z elementu, który już powstał niż pozyskiwać je na nowo z ziemi. Jeśli chodzi o kwestie ochrony środowiska, działalność firm operujących na rynku europejskim reguluje odpowiednie zarządzenie Komisji Europejskiej. W związku ze strategią zrównoważonej i inteligentnej mobilności, do 2050 r. Unia Europejska planuje zredukować emisję gazów cieplarnianych związanych z transportem o 90%. W związku z tym ustalono normy dotyczące wydajności i recyklingu, które muszą spełniać akumulatory. Gdy wejdą w życie, nowe baterie będą musiały zawierać przynajmniej 16 proc. kobaltu pochodzącego z odzysku, 85% takiego ołowiu i po 6% recyklingowanego litu i niklu.
Co odzyskuje się z baterii?
Lit, kobalt, aluminium i stal – oto elementy, które specjalistyczne firmy przede wszystkim starają się odzyskać. Czy rzeczywiście im się udaje? W zakładach Renault we francuskim Flins dzięki metodzie ługowania kwasem z zastosowaniem ultradźwięków udaje się – jak twierdzą przedstawiciele firmy – odzyskać aż 98% litu i 96% kobaltu.
Jak podaje Future Tracker opierając się na opiniach firm Li-Cycle i Umicore, około 95% wszystkich materiałów znajdujących się w akumulatorze pojazdu elektrycznego można już odzyskać. Co więcej, w przeciwieństwie np. do plastiku, nie ma ograniczeń co do tego, ile razy kluczowe minerały w akumulatorach litowo-jonowych można poddać recyklingowi.
„Można je poddawać recyklingowi w nieskończoność bez utraty jakości, dlatego można je wielokrotnie wykorzystywać w nowych zastosowaniach” – mówi Caroline Jacobs, menedżer ds. relacji z mediami w Umicore. „Pozwala to uniknąć niepotrzebnej presji na zasoby naturalne i górnictwo”.
Niestety, według Departamentu Energii Stanów Zjednoczonych (DOE) w 2019 r. zebrano i poddano recyklingowi mniej niż 5% akumulatorów litowo-jonowych. Departament Energii szacuje, że materiały pochodzące z recyklingu mogłyby „zapewnić jedną trzecią zapotrzebowania Stanów Zjednoczonych na materiały katodowe do akumulatorów litowo-jonowych do 2030 r.”.
Ważnym graczem na scenie odzyskiwania surowców z akumulatorów jest Redwood Materials, założona przez JB Straubela, byłego dyrektora ds. technologii w Tesli. „Aby pojazdy elektryczne były w pełni ekologiczne i zrównoważone, powinno się nie tylko zbierać zużyte akumulatory i poddawać je recyklingowi, ale także prowadzić pełną rafinację odzyskiwanych metali, a następnie przekształcanie ich z powrotem w precyzyjne materiały akumulatorowe do ponownego użycia” – wyjaśnia w mailu do Energy Monitor.
Ale recykling jest kosztowny i niełatwy
Tradycyjne, dobrze znane metody recyklingu przeznaczone dla akumulatorów kwasowo-ołowiowych nie są optymalne w przypadku baterii litowo-jonowych. To kwestia innego napięcia, gęstości energii i faktu zastosowania w akumulatorach kwasowo-ołowiowych elektrolitów na bazie wodnego roztworu. Tymczasem akumulatory litowo-jonowe zawierają materiały łatwopalne, natomiast recykling litu stanowi wyzwanie m.in. dlatego, że jest to metal bardzo lekki i reaktywny.
Jak przeprowadzać recykling? Początkowo stosowano metodę wytapiania w wysokiej temperaturze. Niestety – to energochłonna procedura, która nie pozwala na odzyskanie wszystkich cennych materiałów.
Jedną z nowych metod jest proces mokrej chemii, stosowany m.in. przez firmę Li-Cycle współpracującą z LG i General Motors. Akumulatory poddaje się obróbce w procesie rozdrabniania podwodnego. Jego efektem jest „czarna masa” zawierająca najważniejsze materiały. W innym zakładzie wydobywa się z niej minerały. Dzięki tej metodzie poprawia się efektywność odzyskiwania surowców i zmniejsza się ryzyko zapłonu. W tysiącu ton „czarnej masy” jest 278 ton niklu, 55 ton litu i 35 ton kobaltu. Z kolei Volkswagen podaje, że 400-kilogramowy zestaw akumulatorów zawiera 126 kg aluminium, 71 kg grafitu, 41 kg niklu, 37 kg elektrolitu, 22 kg miedzi, 21 kg plastiku, 12 kg manganu, 9 kg kobaltu i tyle samo elementów elektronicznych, a także 8 kg litu i 3 kg stali.
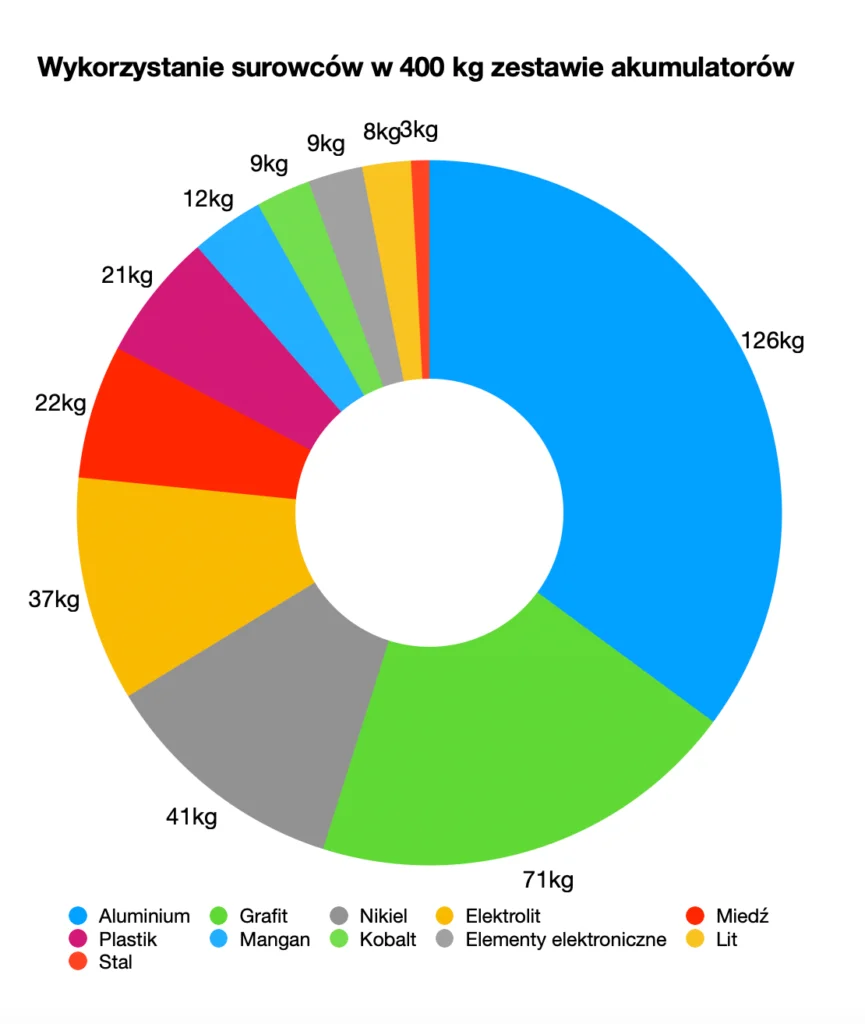
Jak ułatwić proces recyklingu?
Niezbędne będzie tu partnerstwo między producentami samochodów i akumulatorów, jak również zmiana sposobu projektowania baterii. Obecnie nie są konstruowane w sposób, który ułatwia recykling. Priorytetem jest maksymalizacja zasięgu, natomiast nie myśli się obecnie nad tym, jak ułatwić demontaż akumulatora czy jego rozłożenie na części.
Potrzeba uproszczenia całego procesu istnieje – według Departamentu Energii Stanów Zjednoczonych obecnie niski poziom odzyskiwania surowców z akumulatorów można wytłumaczyć ograniczonym łańcuchem dostaw w zakresie gromadzenia, sortowania, przechowywania i transportu zużytych baterii litowo-jonowych, a także kosztem recyklingu w porównaniu z wartością baterii wycofanych z eksploatacji.
Obecna sytuacja recyklingu
Branża odzyskiwania surowców wciąż jest uznawana za raczkującą – należy jednak zauważyć, że dynamicznie się rozwija. W Europie zakłady zajmujące się recyklingiem baterii są w niemal każdym kraju – i znacząca ich liczba znajduje się także w Polsce. Według Battery-Newside liderem jest zakład Minworth (Veolla) w Wielkiej Brytanii, przerabiający 50 000 ton akumulatorów rocznie. W Szwecji w 2030 roku Northvolt zamierza przerabiać aż 125 000 ton. Dziś to 25 000 ton. W Polsce zakład w Zawierciu (Elemental Strategic Metals) odpowiada za 10 000 ton rocznie.
Globalnie, top 10 firm zajmujących się recyklingiem to American Battery Technology Company, American Manganese Inc, Ecobat, Gangfeng Lithium Group Co, LG Energy Solution, Li-Cycle Holding, Lithion Recycling, Redwood Materials, Retriev Technologies i Umicore N.V.
Perspektywy przed recyklingiem
O ile obecnie wciąż poddaje się recyklingowi stosunkowo niewiele akumulatorów, o tyle w przyszłości musi się to zmienić – wynika to zarówno z planów rozwoju producentów, jak i z przepisów. Firma Renault do 2030 r. planuje, by 80 proc. materiałów użytych do budowy akumulatora pochodziło z recyklingu. Według prawa, od 2027 roku nikiel i kobalt mają być poddawane recyklingowi w 90%, a od 2030 roku w 95%. Jeśli chodzi o lit, wartości zostały odpowiednio ustalone na poziomach 50 i 80%.
Według badań, recykling akumulatorów i odzyskiwanie materiałów z nich zmniejsza całościowy ślad węglowy baterii o 17 procent. Obecnie szacuje się, że na produkcję zaledwie 1 kWh ogniw litowo-jonowych emituje się od 175 do 250 kg CO2eq z powodu wydobycia i obróbki surowców, choć nowsze typy baterii o większej gęstości energii pozwalają znacząco zmniejszyć ten parametr. Firma Northvolt planuje w roku 2030 dzięki recyklingowi „zejść” do 10 kg na kWh.
Za sprawą obecnych technologii, po procesie recyklingu, po akumulatorach pozostaje około 30 kg odpadów, w tym ok. 1,8 kg litu, 0,4 kg kobaltu oraz 1,4 kg niklu. Naukowcy pracują obecnie nad nowymi technologiami – m.in. nad separacją za pomocą fal ultradźwiękowych. Ma to być efektywniejsze nawet o 60 proc. w porównaniu ze sposobami stosowanymi dziś. W tym samym okresie będzie się dało przetworzyć nawet 100 razy więcej materiału.
Co dzieje się z surowcami, które zostają odzyskane ze zużytych akumulatorów? Lwia część z nich trafia do ponownego wykorzystania w tym samym celu – czyli ponownie zasilają samochody lub np. elektryczne hulajnogi czy skutery. W przyszłości procent surowców pochodzących z recyklingu ma być w produkcji akumulatorów o wiele wyższy. Jak sprawić, by recykling był prostszy, tańszy i efektywniejszy? Potrzebny tu jest dalszy rozwój technologii pozwalających na skuteczne, ponowne odzyskanie i wykorzystanie surowców, jak również współpraca ze strony firm produkujących baterie – tak, by myśleć o recyklingu jeszcze na etapie projektu. Perspektywy przed branżą są obiecujące… i takie właśnie muszą być. Jeśli elektromobilność ma się rozwijać, musi stać się jeszcze bardziej przyjazna dla środowiska, również w tym aspekcie.
Autor: Mikołaj Adamczuk